Why Caps and Plugs Are a Must-Have for Every Industrial Worksite
For professionals in the industrial sector, ensuring the safety and efficiency of operations is paramount. Caps and plugs play a critical but often overlooked role in maintaining equipment integrity and protecting workers. These small components are vital in preventing accidents, contamination, and damage to machinery. Beyond their immediate functionality, they are essential for adhering to industry standards and regulations. Keep reading to understand why these seemingly inconspicuous items are indispensable for any industrial worksite.
Understanding the Role of Caps and Plugs in Industrial Safety
On an industrial worksite, safety is always the top priority. Caps and plugs contribute significantly to creating a secure environment by covering exposed ends of pipes and tubes, thereby preventing injuries that can be caused by sharp edges. These simple devices also help contain hazardous materials, preventing spills and leaks that could endanger workers and the surrounding environment.
Moreover, by using caps plugs, industries can avoid costly accidents that occur due to contamination or debris entering sensitive equipment. Protective caps and plugs seal off components, ensuring that during storage or transport, the internals remain unexposed to potentially harmful elements. Consequently, this minimizes risk and promotes a culture of safety that permeates throughout all levels of operations.
The role of caps and plugs extends beyond just protection as they can also serve as temporary fixtures during manufacturing processes. They allow for flexible control of workflow, enabling secure pausing and resuming of operations as needed. This adaptability helps prevent the misuse of equipment and can further reduce the likelihood of workplace accidents.
How Caps and Plugs Minimize Contamination Risks on Worksites
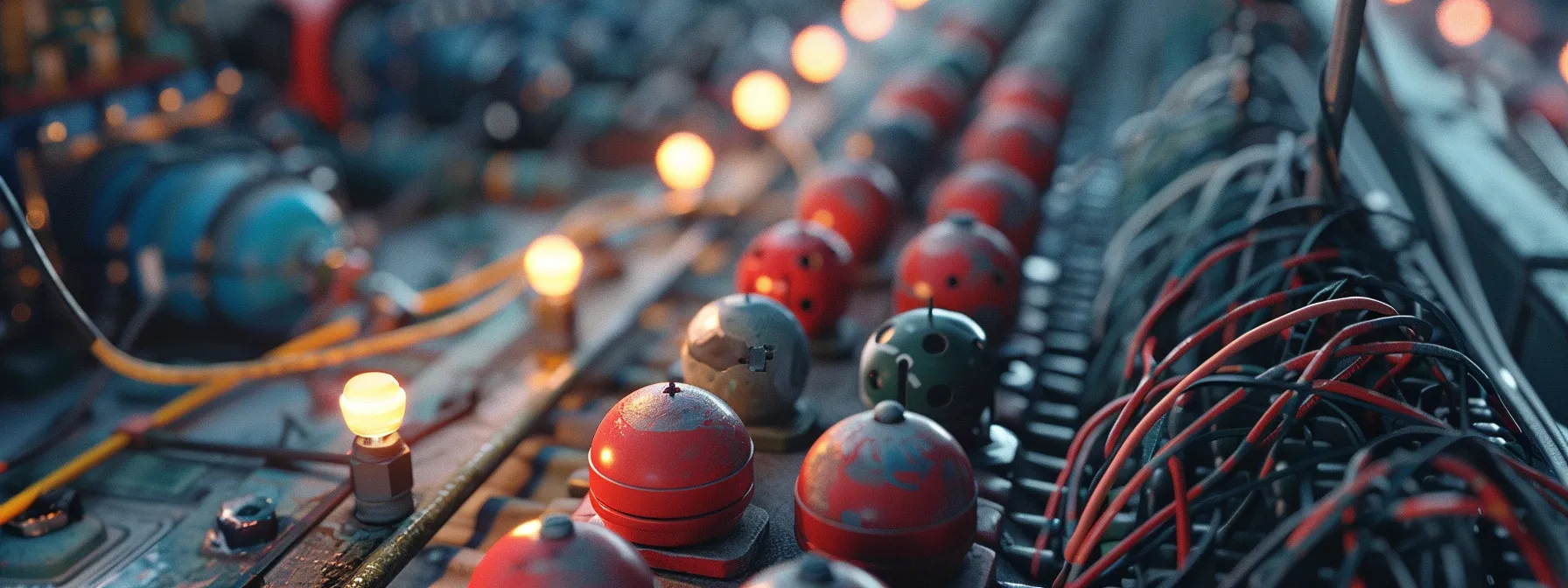
Industrial worksites, by their nature, can be breeding grounds for contaminants. Caps and plugs play an instrumental role in minimizing these risks by providing a barrier against environmental pollutants. Especially in sensitive operations, such as in the food, pharmaceutical, or semiconductor industries, maintaining product purity is non-negotiable.
The intrusion of dust, dirt, and other particulates can lead to product quality issues and even complete batch failures. By employing caps and plugs, companies can protect against these hazards and maintain high cleanliness standards. These sealing solutions are particularly effective during the storage and transport of equipment where exposure risk is elevated.
Moreover, in highly regulated sectors, preventing cross-contamination is not just a matter of best practice but a legal requirement as well. Caps and plugs, when used correctly, keep different substances segregated, ensuring no unintentional mixing occurs. This is essential not only for the safety and quality of the products but also for maintaining compliance with strict industry standards.
Streamlining Maintenance Processes With the Right Protective Components
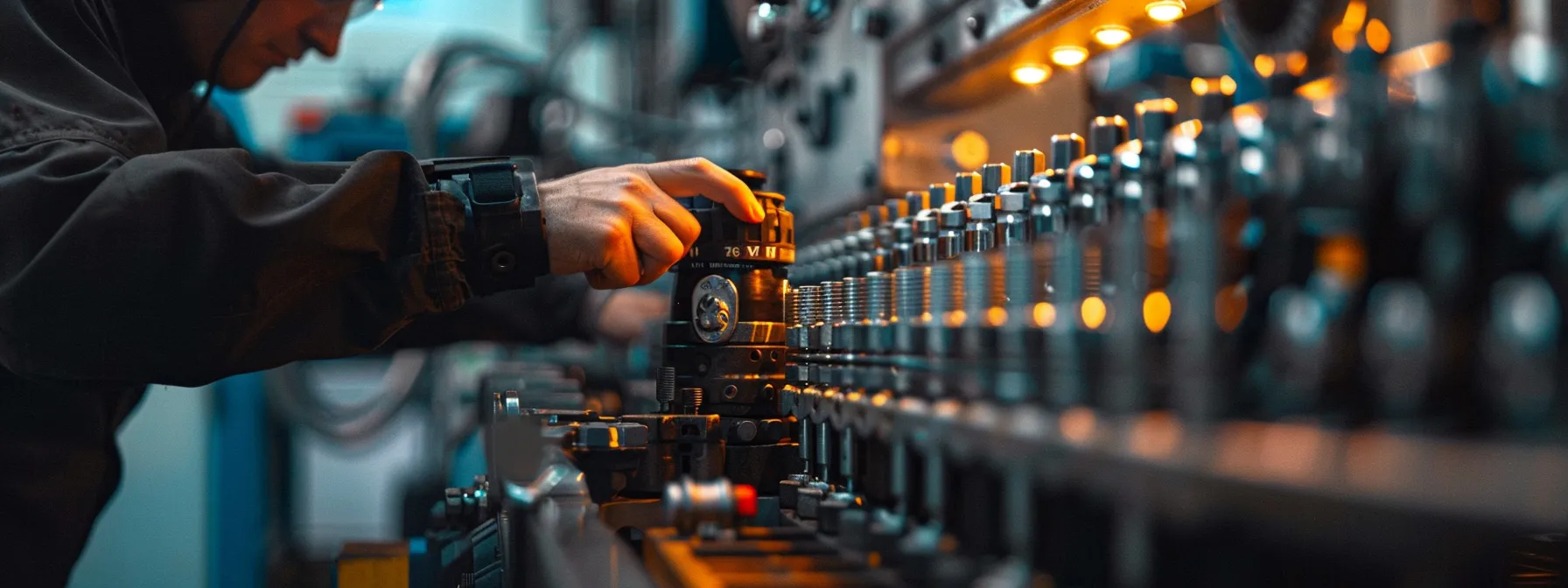
Maintenance is another area where caps and plugs show their value. By simplifying the protective process, they enable a more streamlined maintenance workflow. Caps and plugs are easy to install and remove, facilitating quick access for inspections and repairs. This efficiency aids in reducing maintenance time and ensures that machinery is not out of commission for lengthy periods.
Additionally, using standardized caps and plugs can help maintain an organized work environment. By utilizing color-coding or size specifications, workers can quickly identify the appropriate protective component for each piece of equipment. This organization minimizes human error and expedites maintenance tasks.
Consistency in the use of caps and plugs also contributes to a regular maintenance schedule. Workers are more likely to follow through with protective measures when the process is straightforward, thus increasing the likelihood of preventive maintenance being performed on time. Timely maintenance is key to catching potential issues before they escalate into more significant problems.
Compliance and Standards: The Importance of Caps and Plugs in Industry Regulations
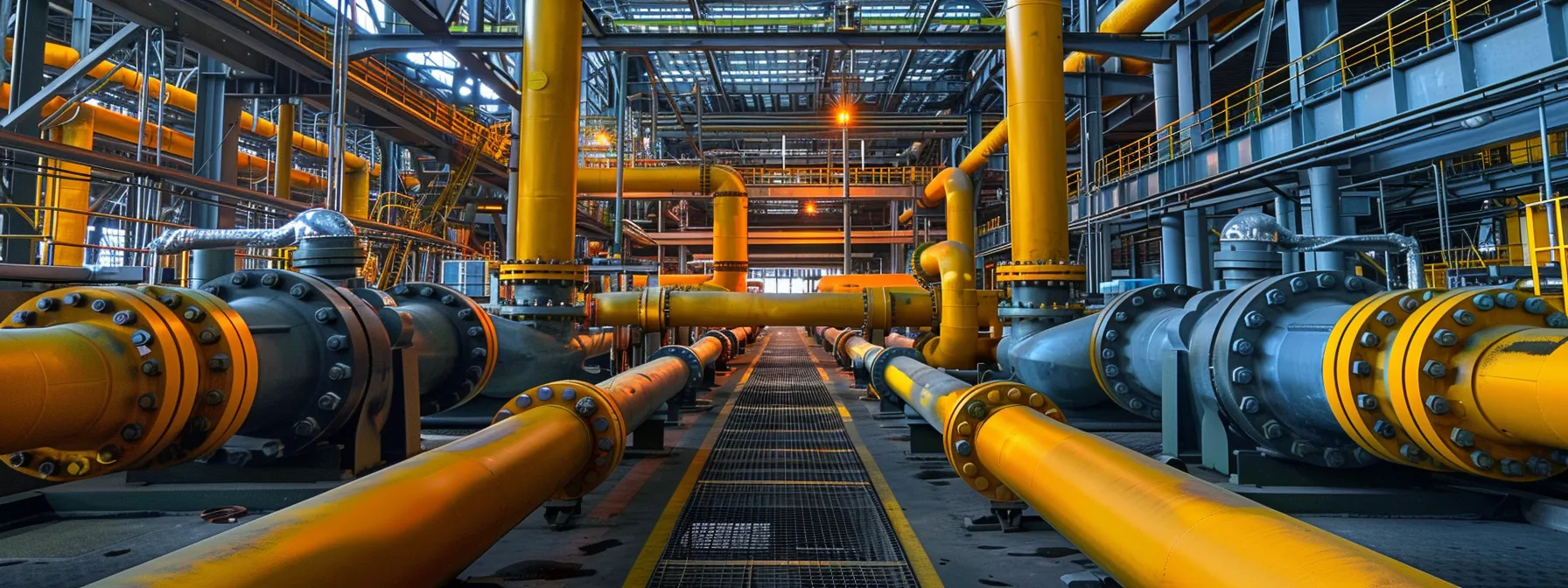
In many industrial environments, caps and plugs are not mere accessories; they are a requirement for compliance with health, safety, and environmental regulations. Understanding the role that these components play in compliance helps emphasize their significance. For instance, in industries dealing with fluids and gases, capped and plugged lines are integral to preventing leaks that could lead to environmental damage or worker exposure to hazardous substances.
Compliance standards often dictate specific materials and designs for caps and plugs to ensure they can adequately perform their functions under diverse conditions. Companies must heed these specifications to avoid regulatory infractions and potential fines. Reliable suppliers of caps and plugs offer products that meet or exceed these regulatory requirements, giving enterprises the necessary peace of mind.
Altogether, the importance of caps and plugs in industrial safety, equipment longevity, contamination prevention, maintenance efficiency, and regulatory compliance cannot be overstated. These small but mighty components play a crucial role in the smooth and safe operation of an industrial worksite. Implementing their use maximizes productivity, protects investments, and ensures a company’s operations are up to the standards of excellence demanded by today’s industries.